ERGONOMICS
The goal of Safety Solutions is to assist you in establishing a safe environment for your business..
When it comes to developing a compliance and ethics program, Safety Solutions will assist you..
QUALITY ASSURANCE
CORPORATE
COMPLIANCE
Safety Solutions is committed to your business quality assurance and quality management..
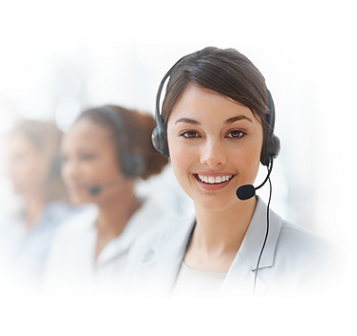
Get More Info!
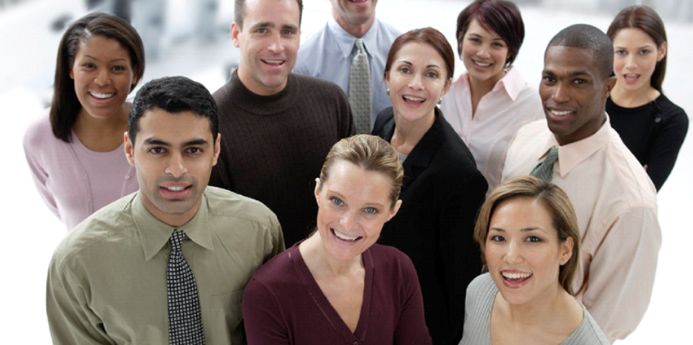
Ergonomics
Human Resources Job Defining Tool
A Study of the Effectiveness of Ergonomically-Based Functional Screening Tests
By Jim Briggs OTR/L, VP Business Development
There are a number of jobs; particularly those with repetitive manual handling that have substantial physical demands. Ideally, the employer is able and willing to reduce these demands through ergonomic job re-designs, where possible. Unfortunately, not all of the demands can be eliminated. People with insufficient physical ability to meet the demands are at increased risk of injury when they are placed on these jobs and they are less likely to stay. As a basic business necessity, employers need long-term employees who can safely perform the job. Physicians, Occupational Therapists and Physical Therapists, as well as many other health care professionals, may be called upon by employers to offer physical ability tests to identify individuals who have the physical capacity to meet the demands of these jobs.
Employers expect the healthcare professionals to offer effective and legal solutions to their problems. Since physical ability test development is not traditionally covered in health care academic courses, therapists and physicians are often unaware of specific legal regulations and the effectiveness of specific types of employment testing. Since some applicants will be denied employment on the basis of these physical ability tests, specific types of validation are required by federal law. This is particularly true of physical ability tests since females and individuals over the age of 40 which are specifically protected from unfair discrimination by law will be less likely to pass a physical abilities test if the job demands are significant thus causing adverse impact. Validation of the test battery, as described in the Uniform Guidelines on Employee Selection Procedures, provides the necessary evidence that any differences in pass rate for protected groups reflect actual differences in ability to safely perform the job.
All employment tests must be in accordance with Title VII of the Civil Rights Act of 1964, the Civil Rights Act of 1991, the Uniform Guidelines on Employee Selection Procedures (29 CFR Part 1607), the Age Discrimination in Employment Act, and the Americans with Disabilities Act. A fundamental requirement common to virtually all employment legislation is that any employment decision-making (Selection) tools must be validated.
The intent of the research reviewed in this article was to validate the effectiveness of ergonomically-based functional screening tests for predicting risk of injury. An ergonomically-based approach can be defined primarily in two ways. First, an ergonomic approach to the job analysis involved directly quantifying the physical demands of the jobs. For example, the heaviest weight routinely handled and how it was handled was quantified, and the aerobic capacity needed to meet the energy expenditure requirement of the job was determined.
One of the strongest study designs for predicting the risk of injury is to give new-hires the test battery, and then place them on the job without regard to their test performance (Rosner, 2000, p. 579-580). The performance on the job is then monitored for those individuals over the course of their employment. Injury rates and retention can then be compared between new-hires who passed the battery and new-hires who failed.
An alternative method for assessing the effectiveness of a testing battery in relation to injury experience is to compare the performance of new-hires who began work before the test battery was implemented to new-hires who began after implementation. This design is referred to hereafter as a “pre/post-implementation analysis.” The major benefit of this study design is that the testing program can be immediately used for making screening decisions rather than waiting until a sufficient sample of new-hires who fail the battery are brought on the job in order to meet the predictive study sample-size requirements. The drawback is that the study design involves comparing performance from two different time periods and different pools of employees. Any other changes between those two periods may impact the ability to detect the effectiveness of the screening program. This issue can be addressed by comparing the groups in relatively tight time periods, such as one year, pre- and post-implementation.
Although the pre/post-implementation analysis design is not as strong relative to a predictive validation study design in providing evidence to make causal inferences concerning the implementation of the program, obtaining a consistent effect size across different populations, industries, settings, and time does provide a strong inference that the observed effects are due to the program and not to artifacts such as regression to the mean and selection bias. Taken together, the results of this type of study can provide a strong inference that the observed effects are due to the implementation of the testing process.
Opportunities arose to perform predictive validation studies of physical ability tests batteries for warehouse jobs in three different industries. The first study focused on the selector job in eleven food distribution warehouses. Over the course of a shift, a selector manually handled thousands of pounds of product. The second study focused on loaders in a soft-drink warehouse. Like the grocery selectors, the loaders built pallets of soft-drink cases, which were then loaded onto outbound delivery trucks. Loaders also manually handled thousands of pounds of product over the course of a shift. The third study focused on de-palletizers and shippers in three retail distribution warehouses. Again, employees in these jobs manually handled thousands of pounds of product over the course of a shift.
After completion of the predictive validation studies, similar test batteries were implemented in other warehouses with similar jobs. Comparisons of injury rates pre- and post-implementation were performed at 175 of these locations.
The process of implementing the physical ability test battery was the same at all locations included in these studies. It consisted of four basic steps. The first step was to ergonomically analyze the job requirements for the purpose of quantifying the strength and endurance demands. The second step consisted of designing a physical ability battery that measured the significant job demands, as documented with the ergonomic job analysis. The third step was to determine the cutoff score for each test. The fourth step was to gather data on injury experience and retention for the study groups, and evaluate the effectiveness of the battery.
Job Analysis: The first step in the job analysis process was to identify those essential functions within the job that appeared to be physically demanding. Physical demands arose both from the performance of specific tasks (e.g., lifting a heavy box), and from the overall physiological impact of all the tasks performed over an entire shift. The overall physiological impact of all the tasks was quantified by measuring the average energy expenditure requirement over the shift.
Strength Demands: Information regarding the strength demands was obtained through interviews with the workers and their supervisors, and by taking measurements of the forces required. This information also included the frequency of handling, how an item was handled, and the region of the body in which it is handled (e.g., floor level, knee level, mid-chest, shoulder and above). Whole-body dynamic strength testing was used in the test battery. This type of strength testing was more functional, and allowed the person to perform the test in the same manner as when lifting on the job.
Isokinetic strength testing was considered, but not elected since it did not reflect the way cases were actually lifted, and required reliance on statistical relationships to justify the test cutoffs. Said another way, Isokinetic strength testing was rejected as an alternative because an actual demonstration of the ability to lift would provide a direct measurement of the ability to meet the strength requirements of the job. Therefore, with the actual demonstration of lifting ability, it was not necessary to rely on statistical extrapolations to determine an individual’s ability to meet the demands of the job.
A second consideration was that whole-body dynamic strength testing offered more opportunity for females and older males to compensate for any differences in isolated muscle strength/weakness relative to younger males. For instance, females and older males, in general, have lower upper-body strength than young males. A whole-body strength test of ability to lift would allow females and older males to compensate for any upper-body weakness by using the legs, so whole-body testing would more directly measure the ability to meet the job requirements and safely perform the given job, and have less adverse impact for females and older males, at least relative to isolated strength testing.
Endurance Demands: The working muscles require oxygen in order to perform the dynamic contractions involved during extended repetitive manual material handling. The energy expenditure requirement is typically measured by determining the amount of oxygen consumed in the course of performing the work. In the jobs of interest in these studies, it was important to be able to study the energy expenditure over the course of the shift.
A step test was administered to each participant to document his or her maximum aerobic capacity. This provided the information needed to document the relationship between heart rate and energy expenditure for that participant. The step test consisted of stepping up and down on a platform of specific size at increasing work rates, while heart-rate was monitored. The test was the same as used in the screening battery. Volunteers performed their normal duties while wearing a heart-rate monitor. The monitor consisted of a transmitter worn across the chest, together with a wrist Mounted receiver. The volunteers were asked to log the start and end times of their major activities while wearing the monitors. At the close of the data collection effort, the accumulated data was analyzed to determine the energy expenditure requirement of the job.
A meta-analysis of the three predictive validation studies indicated that new-hires who passed the battery had a 47% lower worker compensation injury rate and 21% higher retention. A meta-analysis of the 175 pre/post-implementation studies indicated a 41% reduction in worker compensation injuries associated with implementation of ergonomically based physical ability tests..
Click here to learn more about Physical Ability Testing..